As the time approaches for Medicare’s reduced reimbursement rates to take effect as part of the Affordable Care Act, hospitals are under increased pressure to cut back and make themselves more efficient wherever they can. That has meant staff cutbacks for some institutions. But a 10-year old trend of lean healthcare adopted by many hospitals could help healthcare facilities implement practices that could reduce costs and improve efficiency.
In a phone interview with Mark Graban, the chief improvement officer with Kai Nexus and the author of “Lean Hospitals – Improving quality, patient safety and employee engagement,” he suggests some ways hospitals are implementing cost saving measures. “The lean model is about empowering people to improve and making lots of little savings – that’s one of the good things that a lot of hospitals are doing.”
The idea of lean management came from the auto industry as a cost saving exercise developed by Toyota.
Quality control. One of the biggest expenses for hospitals that can be controlled are complications resulting from hospital acquired infections. Graban referenced one hospital that saved $8 million by reducing hospital acquired pressure ulcers. The Pennsylvania Patient Safety Authority also produces reports helping hospitals to reduce hospital acquired infections.
Shift from a project mentality to an efficiency mentality. Graban said, “With the evolution that you see at these really good health systems, it becomes less about doing projects and more about, ‘this is the way we do things now, this is the way we think.'” He identified ThedaCare of Wisconsin and the University of Michigan Health System in Ann Arbor as two hospitals that have embraced change from the top down. “The goal is to have every employee be a problem solver every day.” Graban added that it’s critical for upper management to create an atmosphere where staff at all levels feel that they can contribute and that their contribution is valued.
Small changes can make a significant difference. Just because something needs to be changed doesn’t necessarily mean it has to be a major undertaking. In many cases improvements that can make a difference are subtle differences. Graban recounts one instance in which a hospital had installed an electronic paper towel dispenser right down the hall from a neonatal intensive care unit and its noise caused some disruption. Some staff spoke with the maintenance team and explained why it was a problem and replaced it with a manual dispenser. “That becomes empowering where a hospital allows changes to be made without treating it as a bureaucratic process,” Graban said.
Ask patients. By taking the time to involve patients in the lean process, hospital staff could get insights that may not have occurred to them or get a better sense of their priorities.
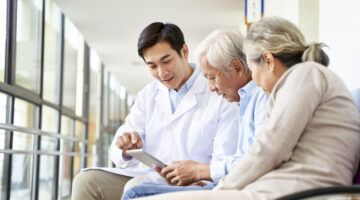
The Human Algorithm: What AI Can’t Replace in Pharma Engagement
At a time when AI is reshaping pharma, Reverba Global CEO Cheryl Lubbert explained in an interview why empathy, context, and ethics still require a human touch.
The biggest concern over cuts in reimbursement at the state and federal levels is it will lead to more staff cuts. Graban said if healthcare systems and hospitals can make significant cost savings with lean techniques, it doesn’t necessarily have to come to that. “The big issue is will hospitals respond and use this pressure to improve or will it drive a lot of dysfunction?”